May 2023- Many of us have heard stories of harmless and amusing laboratory snafus. The chemistry mix-up resulting in smoke, slime, spills, odors, broken glassware, and other near misses. If you can laugh off your lab anecdote with a laugh and happily ever after, consider yourself lucky.
Those who work in a laboratory setting on a daily basis will be the first to tell you that lab safety is no joke, and if not given proper attention, can have dire consequences.
In 1996, the National Safety Council (NSC) established June as “National Safety Month” in the United States. Since laboratories are a more complex environment in terms of worker safety, we thought we’d take a closer look at what goes into developing an effective Safety Program at an Environmental Laboratory.
History of Worker/Workplace Safety
“National Safety Month” is a month-long safety awareness campaign, as NSC and participating organizations strive to increase awareness of common, avoidable safety and health risks, and take steps to decrease the number of unintentional injuries and deaths in the United States.
The State of New Hampshire was actually one of the first states in the union to recognize the need to enact legislation to protect the safety and health of its workers, with some regulations in place as early as 1917.
The Safety & Training Division of the NH Department of Labor administers and enforces laws such as:
RSA 281-A:64 Related to Establishing Safety Programs & Committees
RSA 277 Related to Safety & Health of all Employees throughout NH
RSA 277-A Related to Toxic Substances in the Workplace
ChapterLab 600 Requirements of Safety Programs & Committees
Decades later, in 1970, the United States established the Williams-Steiger Occupational Safety and Health Act, to recognize the necessity for regulations and policies for work safety for all US employees. The Act established the formation of The Occupational Safety & Health Administration (OSHA), which opened its doors in the Spring of 1971 and issued early forms of the standards we know and follow today.
OSHA regulations cover a massive range of general requirements related to worker safety. There are laws related to work surfaces, ventilation, noise exposure, personal protective equipment (PPE), first aid administration, machine operation, container labeling, fire suppression, toxic substances, and much more, with industry specific subsections.
In addition to the standards and guidelines set forth by OSHA, environmental laboratories are also subject to safety related laws and regulations established by governing agencies such as the Environmental Protection Agency (EPA), lab accrediting bodies, and state / municipal environmental departments. Therefore, creating, implementing, managing, and maintaining effective safety policies for a laboratory can be much more complex than for a standard small business such as an office or restaurant.
Standard Operating Procedure & Documentation
In compliance with State, Federal and Industry-specific laws, environmental laboratories must maintain Standard Operating Procedures, or SOPs, related to several areas of the business. An SOP is a detailed, written document with step-by-step instructions describing how to properly perform a given activity.
At our environmental laboratory in Portsmouth, NH, Absolute Resource Associates maintains over 100 different SOPs related to the work we do testing and investigating water, soil, and air samples for environmental contaminants.
Our Safety Committee manages & maintains SOPs specifically related to our Safety Program such as:
- Emergency Action Planning SOP
- Hazard Communication SOP
- Chemical Hygiene SOP
The Safety Committee at ARA also maintains a chemical inventory and SDS file which are updated annually and are easily accessible references for staff. An SDS, or Safety Data Sheet, is a standardized Hazard Communication document detailing the properties of each chemical on site; the physical, health, and environmental hazards; protective measures; and safety precautions for handling, storing, and transporting the chemical.
Safety Plan & Communication
Laws regarding worker safety vary by state. In NH, a company with 15 or more employees must have a written Safety Plan as well as an established Safety Committee which meets regularly. ARA’s Safety Committee is comprised of ten volunteers who meet quarterly, and more frequently if necessary. The Safety Meeting minutes are provided to our entire staff for review and response, with highlights such as key takeaways, safety issues to address or which have recently been addressed. Verbal safety program updates are also given at our regular staff meetings.
Safety Program Snapshot at ARA
One idea that has worked particularly well at ARA has been tasking our monthly internal safety inspection to a rotating member on staff, in order to always have a fresh set of eyes evaluating the facility for safety concerns. What stands out as unsafe by one person may have been previously overlooked by another. This also makes the entire staff feel empowered to participate in keeping our facility and field staff safe.
Regularly surveying all of our processes for safety concerns has been a normal part of the routine at ARA for years now, as we identify issues and adjust where necessary. Other key parts of ARA’s Safety Program include:
- Personal Protective Equipment (PPE): we train each worker about what is required, when it is required, how to use it, how to care for it, PPE disposal guidelines (when and how) etc.
- PPE for lab personnel includes nitrile gloves, chemical resistant sleeves, lab coats or aprons, safety goggles, face shields,
- PPE for our IAQ field staff includes everything from hard hats, gloves, and goggles, to full hazmat protective suits and full-face respirators for sites with potential for asbestos, lead dust, etc.
- In addition to PPE, we must ensure that fire extinguishers, fire blankets, spill or pathogen cleaning kits, eye wash stations and safety showers are located throughout our work space and stocked / functioning properly.
- All company phones are equipped with emergency response contact information.
- Injury reporting or near miss reporting forms are kept at each first aid station.
- Lab surfaces are monitored for Lead, PCBs & other types of contamination.
- We annually monitor respiratory health through test badges worn by employees for a full work period.
- An anemometer is used to be sure our fume hoods are providing correct air flow to allow for the safe use of any chemicals and samples we handle.
- ECD, XRF, and industrial microwave are monitored for radiation leaks.
- Any equipment showing signs of damage or aging which could represent a safety hazard is put out of service and promptly replaced.
- Generalized and task specific safety training is provided to employees starting at the date of hire, and training continues on a regular basis (typically quarterly) throughout a person’s career at ARA.
- Safety Training at ARA covers a wide range of topics including fire response, evacuation procedure, spill clean-up, safe laboratory practices, ergonomics and more.
- Noise levels are monitored to ensure that the equipment we use will not present a threat to workers’ hearing.
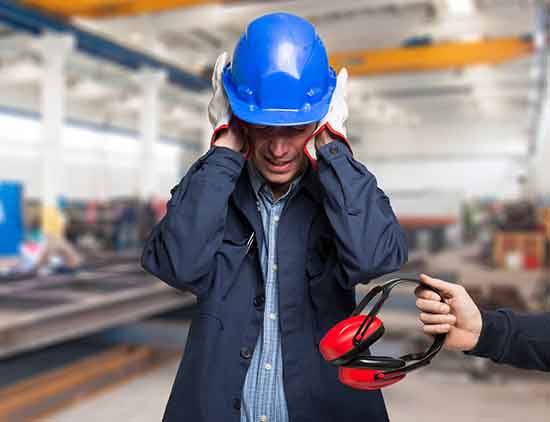
Employee Safety must be part of the Company Culture
Worker safety in a laboratory setting, or any workplace for that matter, is directly proportional to the commitment of employees and management to not only create but implement and adhere to an effective Safety Program. Reflecting on our blog about Company Culture from earlier this year, we realize that our Safety Program is so successful because we are intentional about our culture. Safety is a top priority for everyone at ARA, not just those writing the policies. Looking out for one another, routinely striving to improve our practices, and giving complacency a critical eye is ARA’s recipe for success as a company, as a work culture, and is the backbone of our Safety Program!